Sustainability in Construction: 9 Practices for a Low Impact Build
The concrete jungle is going green and it’s going to help the construction industry stay profitable.
Climate targets are getting stricter, forcing companies to comply or face fines. However, these regulations aren’t simply restrictions. Choosing to employ sustainable practices has a triple benefit to your bottom line:
Environmental protection: Reduce resource use and emissions while meeting regulations and strengthening brand trust.
Economic advantages: Improve long-term profitability through operational efficiency, risk reduction, and investor appeal.
Social responsibility: Boost employee engagement, customer loyalty, and community support by acting ethically and inclusively.
This guide delivers practical strategies for reducing your project's environmental footprint and explains how early decisions lead to long-term cost savings.
The business case for sustainability in preconstruction
Deloitte states that sustainability is becoming a magnet for modern investors and tenants. Over 90% of U.S. engineering and construction firms report that clients are asking for reductions in embodied carbon on projects.
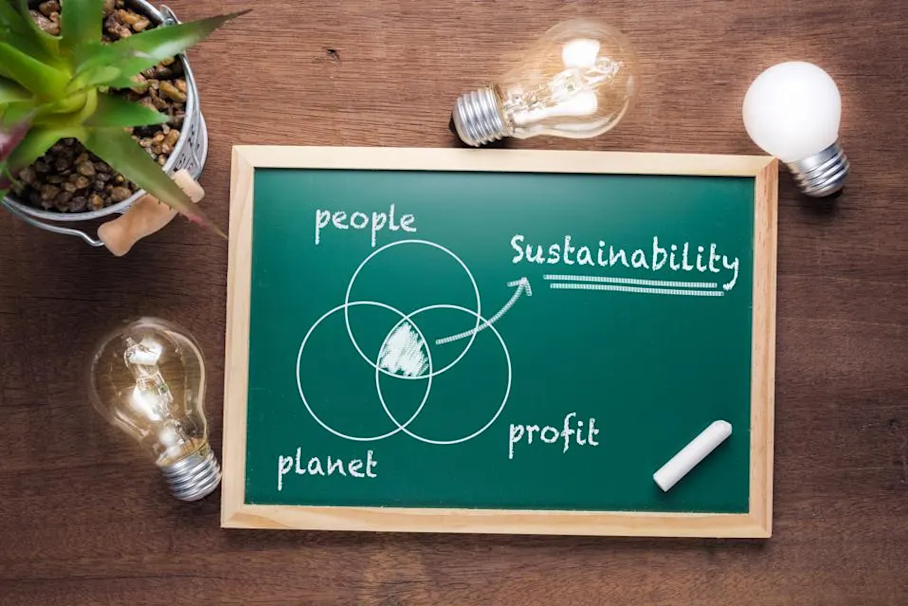
Source: shutterstock
Reduce building lifecycle costs
Energy-efficient designs are a financial strategy. Here’s the proof:
According to the World Green Building Council, most green buildings recover their investment in 3 to 5 years through lower energy and water bills.
In some cases, payback can be even faster—as little as 2 years for office buildings, libraries, and schools, according to the EPA.
Enhance property value and marketability
Sustainability isn’t just a value-add, it’s a market expectation. Certified green buildings command higher rent premiums and enjoy stronger occupancy rates.
Tenants actively prioritize eco-friendly spaces, and developers who invest early in sustainable design typically see faster lease-ups and sales cycles.
Proof in the numbers: A survey by Handelsbanken revealed that over 90% of property investors have received requests from tenants for sustainable features in the past year.
Improve regulatory compliance and future-proofing
From emissions limits to energy efficiency and material sourcing, regulations worldwide are tightening—and fast. According to S&P Global, this shift is one of the top sustainability trends transforming industries through 2025.
Projects that bake in green principles early are naturally aligned with evolving codes, avoiding the headaches (and huge price tags) of retroactive compliance. Mitigate the risk of costly modifications down the line by integrating green principles early.
9 Sustainable practices for preconstruction and construction
Sustainability starts long before the shovel hits the ground. These 9 strategies will help you build responsibly, while keeping your project efficient, cost-effective, and future-ready.
1. Site selection and assessment for sustainability
Where you build matters just as much as how you build. Choosing the right site is your first sustainability decision.
Prioritize locations that minimize environmental disruption by considering:
Access to public transportation to reduce future commuting emissions.
Existing infrastructure to avoid unnecessary new developments.
Natural habitat preservation, ensuring ecosystems are protected and integrated thoughtfully into the project.
Digital tools make site assessment easier. Advanced site surveys and digital twins (like these environmental tags features) provide critical context and visibility from the start. Now, assessments can happen seamlessly across teams anywhere in the world.
2. Prioritize renewable and low-impact materials
When it comes to sustainability, the materials you choose make or break the carbon footprint. Getting it right from the start can drastically change your impact. In fact, embodied carbon can account for over 50% of a building’s total lifecycle emissions, especially in energy-efficient designs.
Here’s how to ensure your materials work for both your project and the planet:
Understand embodied carbon: The carbon footprint of materials, covering everything from production to disposal. Low embodied carbon materials, like timber or recycled content, have a far smaller impact.
Evaluate Environmental Product Declarations (EPDs): EPDs provide transparency, detailing a material's environmental impact, including emissions, water use, and energy consumption.
Track materials with digital twins: Digital twins help monitor materials from sourcing to installation, ensuring all decisions align with sustainability goals and minimizing waste.
TIP: Use “as built” documentation to track every material and organize your documentation logically.
3. Integrate energy-efficient design from the start
Pre-construction simulations help you do hyper-accurate energy modeling for your building’s power sources. Renewable sources like solar design and geothermal systems can easily be simulated for maximum reliability and efficiency.
Check out this video for more information on energy modelling:
Pairing digital twins with IoT technology brings in even more detailed facility controls. Every sensor, system, and performance metric is displayed in real-time, empowering predictive optimization and maintenance.
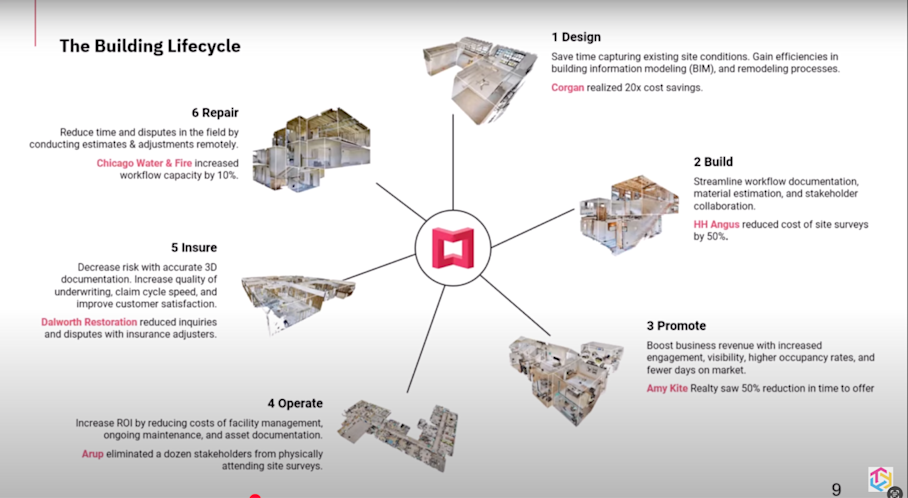
Source: Tavco, Digital Twins for AEC Workflows
4. Plan for waste reduction and resource reuse
Thoughtful planning during preconstruction is the winning shot in your war with excess. By mapping out a waste management strategy early, you’ll reduce landfill contributions, save money, and streamline workflows on site.
Smart waste strategies include:
Preconstruction planning to forecast material needs accurately.
Sourcing recycled or reusable materials wherever possible.
Separating and recycling waste streams during construction.
TIP: BIM clash detection helps you prevent installation errors and waste before construction begins.
5. Align early with certification frameworks
The following frameworks set the gold standard for sustainability:
LEED focuses on measurable performance across energy, water, and material efficiency. Projects earn points for things like smart design, renewable energy, and low-impact materials, with certification levels from Certified to Platinum.
BREEAM takes a broad view of sustainability, scoring projects on everything from energy and materials to health, land use, and local context. It can be applied at different stages, including design, construction, and operation.
Living Building Challenge is the most ambitious. It asks buildings to give more than they take—producing their own energy, managing their own water, and creating positive impacts on people and places.
A digital twin makes cross-functional alignment easier and gives certifiers exactly what they need, without chasing down spreadsheets. Explore this virtual documentation space below:
6. Focus on indoor environmental quality from the outset
From natural light to fresh air, the quality of your indoor environment directly affects health, wellbeing, and productivity. Getting it right means more than meeting code, it means designing for people.
Design moves that matter:
Optimize ventilation and filtration systems to reduce pollutants.
Use low-emitting paints, sealants, and materials to limit VOC exposure.
Factor in daylighting and acoustics for overall comfort.
Integrating with tools like the AWS IoT TwinMaker is like a pulse-check for your building. It shows how air moves, where energy leaks, and what can be improved.
7. Plan water conservation early
Water planning now can future-proof your building against both scarcity and rising costs. For example, companies like Greystar have achieved a 68% reduction in water usage and over £111,000 in savings by adopting water management technology
Design with conservation in mind:
Specify high-efficiency plumbing fixtures and appliances.
Plan for greywater reuse and rainwater capture.
Choose native, drought-tolerant landscaping where applicable.
8. Enable remote collaboration from the beginning
Sometimes the most sustainable thing you can do… is not show up. Virtual site walks and remote coordination mean fewer flights, less commuting, and quicker decisions.
How to design for a leaner process:
Replace early-stage site visits with virtual walkthroughs to save big on your carbon footprint.
Use centralized models to align stakeholders without in-person meetings
Document progress digitally to reduce site access needs
Example in action: Danone used accurate virtual representations of their facilities to streamline decision-making across international teams—cutting down delays, reducing travel, and aligning faster.
9. Design for the building’s full lifecycle
The work doesn’t stop after construction. Make sure you design layouts that can be reconfigured and systems that are easy to upgrade.
Select materials and assemblies that are durable and straightforward to maintain to reduce renovation waste. It’s a good idea to also integrate modular elements that help reduce the need for costly renovations down the line and extend the functional life of the building.
Lastly, track and document as-built conditions from the start. This creates a reliable reference for future teams, making upgrades, maintenance, and repurposing more efficient and less disruptive.
How digital twins enabled Canoa’s low-carbon commercial retrofits
Canoa’s commitment to sustainability is transforming the commercial real-estate sector. Their approach to retrofitting commercial spaces leaned heavily on Matterport’s digital twins, helping them reduce emissions and resource use across every project stage.
Accurate project planning: With precise spatial data captured upfront, Canoa ensured accuracy and reduced the environmental impact from unnecessary travel. Virtually “walking through” a building from anywhere in the world meant teams could plan and make decisions remotely.
Increased efficiency of resource allocation: By having a clear overview of the building’s layout and existing conditions, Canoa avoided over-purchasing or unnecessary demolition.
Improved visibility of inventory and asset management: Canoa was able to move beyond the traditional method of tracking items manually and instead create a digital repository of the building’s assets.
“At the end of the day, it makes sense to delegate this to people who capture spaces for a living so we can focus on what we do best—designing and managing spaces and inventory so our customers can thrive.” Lance Amato, Head of Compliance at Canoa
Check out the video below to learn more:
Use digital twins to make sustainability goals easy
Building sustainably has become a strategic choice that leads to long-term savings, enhanced property value, and a smaller environmental footprint. Canoa is a prime example of the bottom line impact of green facility management using Matterport.
Interested? Chat with an expert.