Wesbuilt Construction: Streamlining Projects with Matterport and Procore
New York Based Contractors sees 61% reduction in document errors and omissions.
Wesbuilt Construction faced challenges in managing complex projects due to space constraints, logistical issues, and the COVID-19 pandemic. They adopted Matterport’s 3D digital twin technology and integrated it with Procore to streamline communication, facilitate remote site walkthroughs, and speed up RFI processing. This solution enhanced collaboration, reduced errors, and improved transparency, cutting project durations by 22%. The technology also provided valuable post-construction asset management and helped Wesbuilt secure new projects, reducing claims by 17% and boosting business growth. The integration resulted in more efficient workflows, faster decision-making, and significant time and cost savings.
Matterport helps construction teams capture, document, and coordinate on-site conditions and project milestones with 3D visual clarity. Learn more about our solution here.
Customer Results Summary:
61% reduction in document errors and omissions
36% reduction in hours spent on rework
22% reduction in project duration
17% fewer claims / litigation
Challenge
Wesbuilt Construction, a New York City-based general contractor and construction management firm, encountered several typical challenges that arise in large, complex construction projects. These challenges were further amplified due to the firm's operations in a dense urban environment, where construction projects must account for limited space, logistical obstacles, and strict timelines. Wesbuilt needed a way to manage these challenges efficiently, especially when dealing with multiple stakeholders such as owners, architects, engineers, and subcontractors.
Communication, in particular, was a major pain point for the Wesbuilt team. Construction projects often generate a constant stream of RFIs (Requests for Information), observations, and other issues that require rapid decision-making. In traditional workflows, RFIs would involve extensive back-and-forth exchanges via phone calls, emails, and site visits, which not only slowed down project progress but also introduced the risk of miscommunication or incomplete information. The lack of real-time access to visual data compounded this problem, making it difficult for architects and engineers to address on-site issues accurately and efficiently.
Further complicating matters, the COVID-19 pandemic created a situation where physical site visits and in-person meetings were no longer feasible. This was a significant challenge for Wesbuilt, as their project management processes had previously relied heavily on regular on-site walkthroughs with architects and clients. Weekly or bi-weekly meetings were a key part of ensuring project transparency and alignment among all stakeholders, but travel restrictions made these impossible. For architects located hours away from the project site, the inability to visit the site in person added even more delays to decision-making processes.
In this environment, Wesbuilt recognized the urgent need for a digital solution that would allow them to continue operating effectively. They needed a platform that could centralize project data, facilitate communication between teams, and offer remote access to the site. Most importantly, the solution needed to maintain accuracy and clarity, ensuring that project progress could be tracked and monitored without sacrificing the quality of the work.
Solution
To address these challenges, Wesbuilt Construction turned to Matterport’s Reality Capture technology, which provided them with the ability to capture immersive 3D digital twins of their construction sites. This 3D modeling solution allowed Wesbuilt to document every stage of the project visually and in precise detail. Furthermore, they integrated Matterport with Procore’s construction management platform, which helped centralize all project-related information, enabling efficient communication and project oversight.
Remote Access and Collaboration: One of the most immediate benefits of implementing Matterport was the ability to conduct virtual site walkthroughs. Using Matterport’s digital twin technology, Wesbuilt could provide project teams and clients with a highly accurate, visual representation of the construction site, allowing them to access it remotely. This was particularly valuable during the pandemic, where restrictions on physical site visits could have otherwise caused major project delays. By using the 3D scans, stakeholders could virtually navigate the space from their homes or offices and review progress without having to be on-site. This capability kept the project moving forward and ensured that regular meetings could still take place, albeit virtually.
Efficient RFI and Observation Tracking: The integration of Matterport and Procore enabled Wesbuilt to streamline their RFI and observation workflows significantly. Instead of relying on phone calls or emails, RFIs could be generated directly from the Matterport scan and automatically synced with Procore. The visual context provided by the 3D model made it easier for the design team and project managers to understand issues, speeding up response times. For instance, the ability to tag areas within the 3D model meant that teams no longer had to rely solely on written descriptions or 2D images to identify issues. Instead, they could view the exact location and context of the problem within the virtual environment, allowing for more precise and efficient communication.
Regular Site Documentation and Progress Monitoring: Wesbuilt employed Matterport for regular bi-weekly scans of their construction sites to document progress and milestone completions. These scans were automatically uploaded into Procore, providing all stakeholders with real-time access to the latest site data. The ability to reference previous scans allowed project teams to track changes over time, compare past and current conditions, and ensure that work was progressing according to schedule. For clients who were located remotely, this meant they could monitor the project's development without needing to physically visit the site, saving time and resources. Additionally, the archived scans created a permanent record of the project’s development, which could be revisited if any issues arose down the line.
Closeout Model and Asset Management: As the project approached its conclusion, Wesbuilt created an interactive facility asset model using Matterport’s tagging functionality. This model allowed them to document key aspects of the project, such as manufacturer details, product specifications, and as-built conditions. By embedding all of this critical information directly into the 3D digital twin, Wesbuilt ensured that the facility management team had a comprehensive and easily accessible record of the building’s systems. This model became an invaluable resource for ongoing maintenance, future renovations, and any potential troubleshooting, as it provided an accurate and detailed view of the building's infrastructure long after the project had been completed.
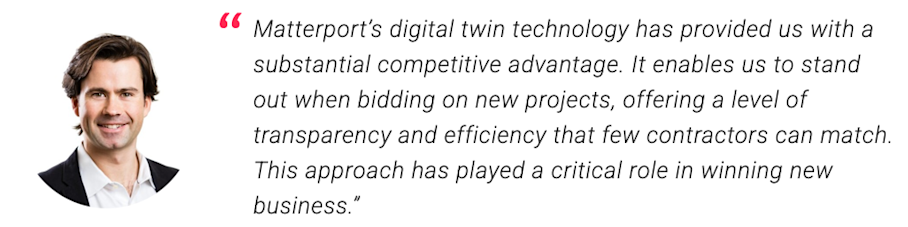
Results
The integration of Matterport and Procore delivered several measurable benefits to Wesbuilt, providing both immediate improvements to project workflows and long-term advantages that extended beyond the construction phase:
Enhanced Remote Collaboration: During the pandemic, the ability to conduct virtual site walkthroughs proved invaluable. Architects, clients, and other stakeholders could now participate in project updates remotely, saving time and reducing travel requirements. With frequent check-ins facilitated through virtual meetings and Matterport’s immersive 3D models, Wesbuilt ensured decisions were made faster, minimizing disruptions to the project schedule.
Faster RFI Processing: By integrating Matterport’s visual data into Procore, Wesbuilt was able to drastically reduce the time it took to process RFIs and resolve on-site issues. In the past, generating an RFI involved multiple exchanges of emails and phone calls. However, with the ability to create RFIs directly within the 3D model and sync them with Procore, issues could be resolved almost immediately. This led to a 61% reduction in document errors and omissions, improving the overall efficiency of the project team.
Improved Project Transparency: One of the key advantages of using Matterport’s 3D models was the transparency it provided to clients and stakeholders. With real-time access to project progress, stakeholders were able to monitor milestones and stay informed at every stage. This was particularly beneficial for remotely located owners or architects, who could engage in the project without visiting the site. As a result, Wesbuilt experienced a 36% reduction in rework, as issues were identified and addressed earlier in the process.
Comprehensive Closeout Documentation: The closeout model created by Wesbuilt, which incorporated key asset information into the 3D digital twin, provided lasting value for the client. The facility management team could easily access detailed records, such as product specifications, as-built conditions, and maintenance information. This documentation proved especially useful in maintaining the building efficiently and minimizing future disruptions.
Reduced Project Duration: By streamlining communication and improving collaboration between teams, Wesbuilt saw a 22% reduction in overall project duration. The ability to coordinate remotely, resolve RFIs faster, and eliminate unnecessary site visits contributed to keeping the project timeline on track and reducing delays.
Competitive Differentiation and Business Growth: Wesbuilt also found that using Matterport and Procore helped them win new projects. Clients appreciated the firm’s use of innovative technology to deliver greater project transparency and efficiency. Additionally, the streamlined workflows reduced the number of disputes and misunderstandings on projects, resulting in 17% fewer claims and litigation. This differentiator helped Wesbuilt secure new contracts and expand its client base, as more and more clients recognized the value of having a comprehensive, digitally managed construction process.
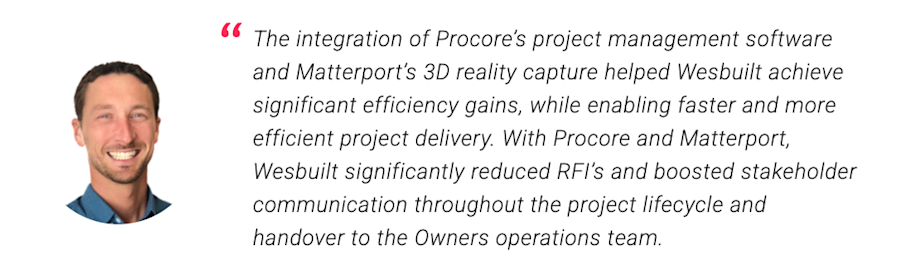
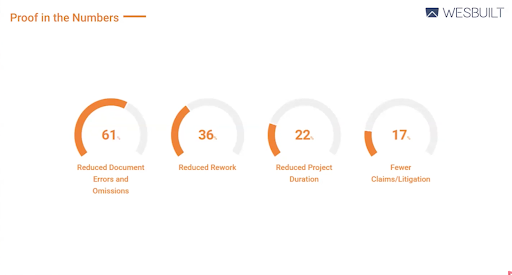
Learn more about the Matterport and Procore partnership here.